Safety should always be a top priority when working in any research facility, but safety is especially critical in an extraction lab. No matter which extraction equipment and processes you’re using, there are always risks of danger. However, by taking the right precautions, you can ensure that you not only manufacture quality products, but also protect the safety of your employees.
Safety concerns in a botanical extraction facility
Quite a few dangers exist in an extraction lab. After all, your employees are working with chemicals and large-scale equipment, both of which can present their own hazards. Facilities should consider the following safety concerns while writing their standard operating procedures (SOPs):
Fires or explosions:
Working with solvents, various temperatures and pressure there’s always the risk of explosion or fire. Especially when machinery is not correctly set up and employees are not adequately trained. Extractors should always thoroughly research their machinery to ensure it comes from a reliable source and never use DIY production techniques that could put personnel at risk.
Harmful vapor:
The process of botanical extraction involves flammable liquids and gasses that can produce toxic vapors if not properly controlled and stored. Facilities need to ensure that their machinery is functioning correctly and not emitting vapors that it shouldn’t. Adequate personal protective equipment (PPE) should be provided to staff so that employees are not inhaling excessive amounts of these vapors during the extraction process. Of course, proper procedures should be developed to train personnel on what to do if harmful vapors are detected.
Machinery malfunctions:
It is essential to ensure that all the equipment in an extraction facility is CE certified. Third-party inspections and testing services ensure that processes and products meet quality and safety standards for consumers and personnel.
Hearing loss:
The machines in an extraction facility may operate at very loud volumes, potentially exposing operators to hearing loss. Without protective equipment for their ears, hearing loss is one of the most overlooked safety concerns within extraction facilities.
How to improve the safety of your botanical extraction facility
Although these safety risks are real and consequences often severe, there are things manufacturers can do to mitigate them and improve the safety of their botanical extraction facility. These simple and secure ways can prevent accidents, injury, and illness. Consider the following methods to improve safety in your extraction lab.
Use third-party tested equipment:
Obtaining testing or purchasing pre-tested equipment that is CE certified or GMP compliant is essential to ensuring the safety of your facility and employees. Equipment tested and verified by a third party helps prevent fires, explosions and malfunctions.
Set up shop in a well-ventilated facility:
Establishing and monitoring ventilation systems is a simple way to prevent explosions and fires. Proper ventilation also helps protect employees from respiratory issues, minimizes risk of potentially harmful exposure, and reduces the amount of dust accumulation that could lead to equipment damage that can put people’s safety at risk.
Establish safety SOPs and train employees:
Training and re-training employees is the best albeit intensive way to ensure they know how to conduct the extraction processes in a safe manner. Employees should understand the common safety hazards within a facility, including exposure areas and what to do if an accident occurs.
Provide appropriate PPE for employees:
Ensuring that your employees have the proper PPE will help eliminate the risks and dangers of extraction facilities. NIOSH-approved N95 disposable respirators, for example, can help to reduce exposure to botanical dust that causes respiratory issues. Earmuffs and earplugs can help avoid hearing damage or loss as well.
Extract in the right environment:
Not all extraction processes require the same environment. Manufacturing spaces referred to as Class 1, Division 1 rooms are built with fire-suppressing materials and designed to ventilate potentially flammable gases, such as hydrocarbons. In C1D2 rooms, hazardous gases are usually confined within closed containers or closed systems from which they can escape only in the case of accidental rupture or breakdown. Typically, if a facility is conducting botanical extraction with butane, propane, or isobutane, it will require a C1D1 classified room. If your facility’s primary function is botanical extraction with ethanol solvent using a centrifuge, you’ll need a C1D2 space.
Obtain certifications:
Most ethanol and hydrocarbon labs require a Lower Explosive Limit (LEL) rating. In general, LEL ratings identify hazardous levels of combustible gas or solvent vapor in air, expressed as “% LEL.”
Even with these measures, however, safety and accident prevention is an ongoing and evolving process. Manufacturers should always continue to test, revisit, and update their procedures and standards over time. The following are all great measures to ensure your facilities continues to run safely under your current standards:
• Regular training and drills
• Employee surveys to understand what personnel are observing
• Regular third-party inspections
• Obtaining proper GMP certification
• Providing protective equipment
• Establishing safety SOPs and emergency measures
• Thorough documentation of processes
Why safety is important in botanical extraction facilities
Safety is essential in botanical extraction facilities for a variety of reasons. Practicing safety measures such as regular training and testing not only protects human health but helps to avoid lawsuits and fines as well. Overall, safety guidelines within your facilities are critical for the following reasons:
• Protecting human health and safety
• Protecting your company’s reputation
• Meeting GMP standards for accreditation
• Protecting your assets (equipment and product)
• Avoiding lawsuits and fines
While investing in safety upfront may seem time-consuming or expensive, in the long run it protects personnel, brand reputation, and saves money by preserving your facility, equipment, and product and. A strict approach to safety and emergency preparation also helps avoid lawsuits and fines, which can become very expensive.
Staying safe in your manufacturing process
Any company building or expanding a current extraction facility should focus on proper safety protocols. And because standards are ever-changing as the industry progresses, it is imperative to stay up to date. When working with an equipment supplier, it’s important to understand that the hardware they provide meets all current safety standards. Moreover, it’s best to choose a partner with experience in the extraction industry that can help you get your extraction lab started the right way. If you’re looking for the type of supplier who’s ready to offer you insight into decades of experience in botanical manufacturing, look no further than Holland Green Science.
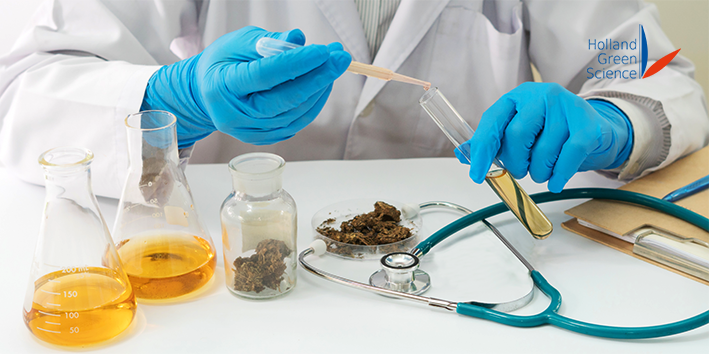